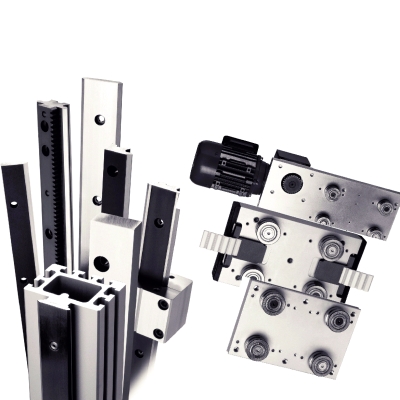
Increased service life with the HepcoMotion GV3 linear system
5 Reviews :
/The frequent failures of the belt sander's linear travel system have been prevented by the use of the HepcoMotion GV3 system, resulting in a 90% reduction in maintenance costs.
The linear travel system with closed ball circulation at Hermes Abrasives was developed for the belt grinder and was able to meet all load requirements. However, this did not stop its frequent breakdowns, which even happened every two weeks. The total costs were significant. Replacing a single element cost a total of about 8% of the annual budget for the maintenance of equipment, plus the cost of downtime for each failure. This was coupled with the need to maintain our own bearing warehouse for future failures.
The solution came from a Hermes engineer who already had experience with Hepco rope systems and "V" guides. By using the GV3 Hepco system, repair costs have been reduced by more than 90% and the company is satisfied with the significant increase in device efficiency.
The British subsidiary of Hermes Abrasives, located in Colchester, is part of an international corporation that is currently the third largest producer of friction products in the world. The factory, which has over 5,000 square meters, is responsible for transforming the friction medium into finished products, 60% of which are returned to the German market for sale on the primary market.
The scope of production is large, from ground products used in finishing in the automotive industry to 1600 mm wide friction belts used in the automatic processing of steel and wood. A typical application for these products are Ellesco grinding and abrasive machines.
The pre-cut lengths of sandpaper are manually clamped into a holder and then automatically transported to the machine using two Hepco GV3 linear guides. The machine is designed to produce perfectly overlapping welds in a belt where any defects could affect the parts being manufactured. John Tilbrook, Labor Director, confirms that "Cutting the friction material is simple, the high level lies in the right connections."
Alumina, silicon carbide, and ceramics are common abrasives on a variety of substrates used in the manufacture of abrasive belts. A particularly aggressive coating has the patented by Hermes-Hermasit, which contains abrasive balls that are perfect for grinding high-quality finishes. All abrasives produce dust that can cause severe mechanical damage.
The size of a single particle of abrasive grain ranges from 16 units to the most aggressive - 2500, which can be compared to flour. The tiniest dust can be the most damaging when combined with a grease to form an abrasive paste. For this reason Hermes prefers systems that run dry, the renowned GV3 Hepco system quality that provides smooth and almost friction-free movement without the need for lubrication.
"It only takes a minute for the contaminants to get into the closed-ball circulation line system, and that's enough to cause problems at startup." John Tillbrook explains. "Basically the system seizes inside and damage to the bearings is only a matter of time" At first Hermes thought the failures were caused by too much stress and tried to correct the problem by initially placing additional bearings on each rail and then doubling the number of bearings. . This caused alignment problems, the actual load carrying capacity increased, but the mean time between failures decreased. Mounting the bearings on a rubber washer helped with this, but the frequent failures were repeated. John Tilbrook continues, "We did not take into account the fact that the closed ball system was not suitable for this application."
One of the key advantages of replacing the old system with the GV3 system was its "V" guides. This caused all debris to actually fall off the guide, unlike the old system which acted as a container, actually blocking all gaps.
Another big benefit of using the GV3 is the combination of concentric and eccentric rollers that allow easy system tuning and reduced wear; none of the closed ball circulating systems has this capability. Hepco Roller Guards, by physically protecting against contamination, also contribute to extending the uptime of Hermes' GV3 installation.
Thanks to these features, the original Hepco rollers had to be replaced after almost a year. "We were spending approximately £ 6,000 a year to maintain a closed ball system - with Hepco our costs were reduced to £ 600," concludes John Tilbrook. "The GV3 system has proven to be a highly effective solution for our company."